The work carried out at the Risk Research Facility (SPARK) is part of the overall strategy of the LSR and focuses on the hazard, which is the component of the risk that physically characterizes the dangerous phenomenon, and according to two application fields
- Natural risks: natural events such as forest fires
- Technological risks: major technological accidents related to the processing, storage and transport of chemicals: fire, explosion, atmospheric and aquatic dispersion
The work carried out in this area proposes an approach with a dual purpose: finalized, since it aims to study phenomena and their impacts on the environment on a laboratory or large scale; and fundamental, since it aims to study the physical or chemical mechanisms involved. This research integrates modeling aspects, either by classical approaches such as numerical or analytical simulation, but also by less classical approaches based on statistical modeling combined with neural networks and cellular automata. The new knowledge and its implementation should allow one to propose operational tools adapted to the constraints of the emergency (speed of calculation, precision and reliability of the results) as well as to complex environments (industrial sites).
Activities: expert industrial risk assessment: fire / flammability (materials, oils, boilover); explosions (gas, dust; BLEVE); leaks of gases or liquids; atmospheric dispersion; blowouts; accidental water pollution.
Objectives: understanding and modelling accidental phenomena linked to industrial risks; studying and proposing technological solutions to plan for and reduce the consequences of dangerous phenomena.
Main equipement and techniques
- Phantom V711, V2512 and Photron SA3 high-speed cameras
- FLIR SC4000 high-speed IR camera and FLIR GASFIND gas detection camera
- Dantec granulometry and 2D speed particle dynamics analyzer
- Full PIV (Particle Image Velocimetry) system
- TRPIV lasers NdYAG 532 nm 15Hz 200 mJ and NdYLF 527 nm 1000 Hz 15 mJ
- Lasers Verdi 532 nm 2W and 5W
- Explosion measurement chain with HBM high-speed data acquisition system and
PCB sensors - Captec radiant and total heat flux sensors
- FARO 3D laser scanner
- Networks of PID detectors and FID analyzers for gas clouds
- Thermal Analysis coupled with FTIR Spectrometry
- 1x1 m sample surface electric / gas-fired radiant panel
- Pyrolysis-GC/MS
- Microscale combustion calorimetry
- Cone calorimetry coupled to FTIR Spectrometry
- Limiting Oxygen Index
- UL94 vertical flame testing
- Hot wire and pilot tube anemometers
Activities and fields of application
- Expert assessment
- Collaborative research
- Feasibility studies
- Design of prototypes
In the fields of:
- Energy
- Petrochemicals
- Chemicals
- Materials
- Nuclear Industry
- Pharmaceutical Industry
- Civil Security
Scientific expertise & Knowhow
Expert assessment for the conducting of dangerous tests
Rapid, distributed, synchronised metrology
Multi-scale testing (laboratory, testing facility and in the field)
Formulation and characterisation of fire-resistant materials
Recent projects
Dust explosions are feared phenomena in industrial installations where powdery materials can be put in suspension. In the context of nuclear decommissioning or the ITER program, dusts (mainly graphite particles or metallic compounds) can be put in suspension and be the source of an explosion. The intensity of a dust explosion is directly related to the propagation of the flame in the reaction medium. The essential parameters of this phenomenon are related to the nature and concentration of the particles, but also to the initial turbulence. In the case of metals, the propagation mechanisms are extremely complex.
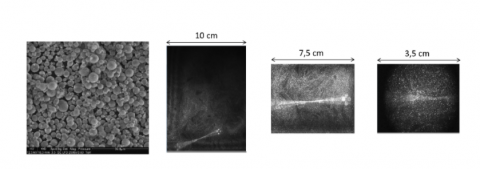
The main objective of this project is to understand the flame propagation mechanisms in the case of aluminum dust explosion and to measure the turbulence and the flame propagation speed. Numerous optical techniques were used (PIV, TR-PIV, umbroscopy, strioscopy), some of which were difficult to implement (use of optical filters and synchronized pulsed lasers).
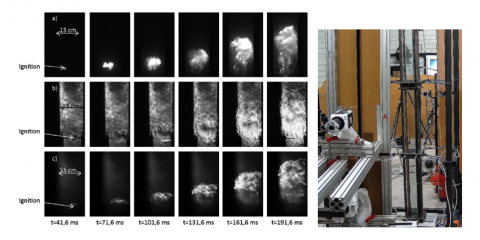
Climate change can increase the risk of drought, and consequently the risk of forest fires. Moreover, the risk of forest fire is also accentuated by the growth of urbanization and the multiplication of the habitat in contact with the forest domain.
LPG is a fuel that can be used in the habitat for cooking, heating and sanitary water. In this case, the LPG is stored near the houses in pressurized tanks of 1 to 2m3 of capacity.
The question of the risk of forest fires in relation to this technological target may then arise. What happens if a forest fire occurs in the urbanized area where LPG tanks are present? Firemen are unaware of the presence of LPG tanks and may be endangered by this risk.
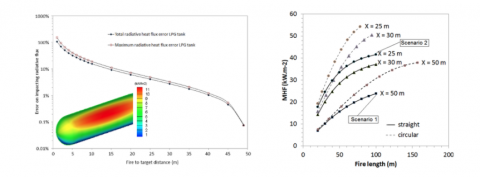
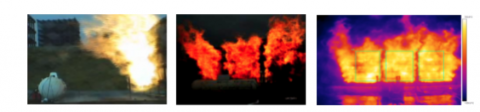
The thermal-hydraulic behavior of the propane tank was modeled in collaboration with the University of Bologna. The aim was to model all the phenomena involved (heat transfer, boiling, convection, evaporation, condensation in the tank) in detail.
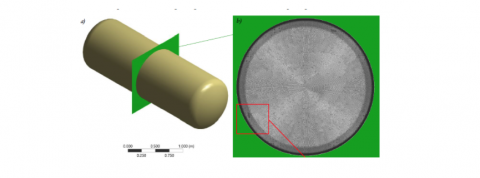
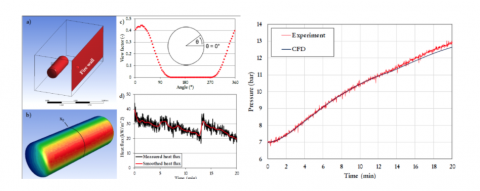
Water is a heat transfer fluid widely used in the nuclear sector but also in other industrial sectors (refineries for example). In a nuclear power plant, water is used in the primary and secondary circuits at very high temperatures and pressures, typically 300°C and a hundred bars. If a leak occurs accidentally in one of the two circuits, the pressure will drop rapidly and the water will overheat. An explosive phase change (BLEVE) with important effects in terms of air overpressure can be feared.
The aim of this research work was to understand what could happen in a scenario of water brought to a high temperature and rapidly depressurized. Little experimental data being available, tests were thus carried out by designing a massive prototype allowing water to be brought to 300°C under saturation conditions, to cause a depressurization by rupture of a calibrated disc and to measure the thermodynamic conditions (P,T) of water during the rupture. Aerial overpressure measurements and high-speed video were synchronized to collect all the data necessary to understand the observed phenomenon.
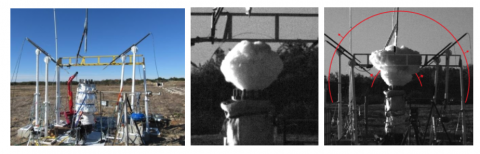
Gas and hydrocarbon fires are the most common scenario in the oil industry. The combustion of these species in liquid, liquefied under pressure or gaseous form can occur following an accidental leak, and can take the form of a slick fire or a flaming jet.
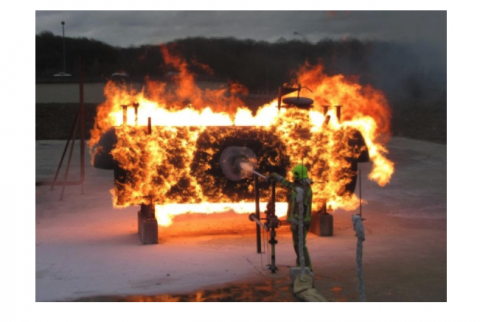
This research project aimed at studying the mitigation of fires by chemical agents, according to a mechanism of inhibition or masking by screen effect.
In the case of a storage containing a liquid at ambient temperature and pressure, the loss of containment leads to a leakage of the liquid on the ground. Retention basins are generally implemented in order to contain the liquid spill. In the case of a volatile liquid, significant evaporation can occur and be the source of a vapour cloud that can be toxic or flammable. A literature review showed that the modeling of evaporation in a bowl configuration was not taken into account in this industrial risk framework. The work showed the important influence of the edge of the basin on the evaporation hydrodynamics; this aspect induces a decrease of the evaporation compared to an evaporation on the open surface.
A focus was also made on the thermal aspect of evaporation. This phenomenon being endothermic, horizontal and vertical temperature gradients appear and Rayleigh-Benard-Marangoni instabilities appear. These thermal phenomena are not taken into account in current models. The results allowed the accessing of the temperature stratification in the liquid. The impact of these phenomena has been quantified and a sensitivity study of the existing models with respect to the deviations due to these points has been performed.
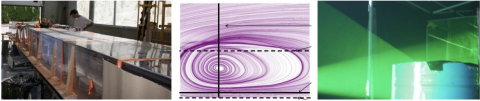
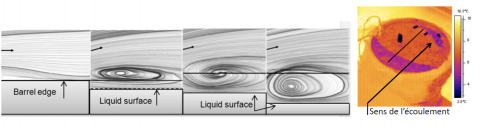
The case of an attack by an explosion is made by means of three vectors: an air overpressure wave, a thermal flow and fragments. The fragments generally come from the source of the explosion or from solids present on site and propelled by the explosion. The case of an attack on a storage facility by only one of these three vectors has been studied in the literature. No publication reported the study of two or three vectors considered in the same scenario however. This work consisted in studying the combination of a fragment (and thus formation of a liquid jet) in interaction with an air overpressure wave, i.e. two coupled attack vectors. The study was carried out using the shock tube of the SPARK platform.
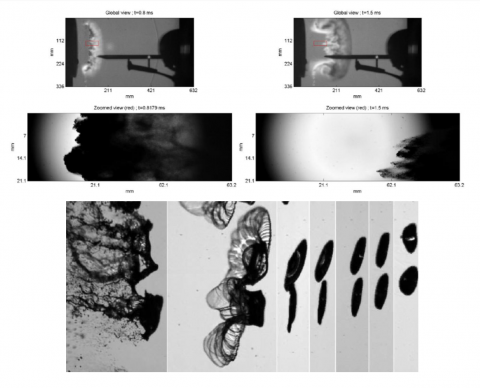
Two essential pieces of information were sought: the fragmentation mechanism and the ultimate size of the drops after fragmentation. Several optical techniques were used to understand the phenomenon: umbroscopy, TR-PIV, laser doppler anemometry, holography.
The BLEVE is a physical explosion that can occur when a pressurized liquefied gas storage is subjected to a thermal flow. The increase in wall and fluid temperature leads to a rupture of the containment when the liquefied gas is overheated. The gas can then change phase abruptly and cause serious effects in terms of overpressure and fragments.
Several models for predicting consequences exist in the far field: they are based on a macroscopic approach considering the mechanical energy that can be released by the gas phase and the liquid phase, converted into TNT equivalents with the use of related charts.
However, these simple approaches are not adapted to the near field (typically 50m). Work has therefore been undertaken to study the BLEVE phenomenon in the near field.
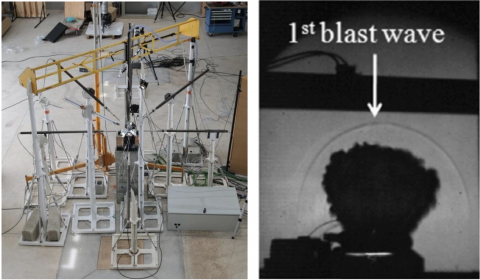
Several experimental campaigns have been carried out in order to understand the complex physics occurring during a BLEVE. Contrary to the far field, the near field requires to understand how the multiple overpressure waves are created by the expansion of the vapour sky and the explosive phase change of the liquid. At the same time, the phase change dynamics and the rate at which the fluid is released drives the force exerted by the tank on the ground.
In the scenario of a propane leak, the most feared scenario is the formation of a gas cloud and its delayed ignition. The more the ignition is delayed, the larger the cloud will be and the more dramatic its explosion will be. It appeared that little knowledge was available on the effects of cloud geometry on the explosion dynamics. Indeed, the hypothesis most often used is that of a hemispherical cloud with an ignition at the periphery of the cloud. Research work was thus undertaken focusing on the influence of the shape of the gas cloud on the combustion dynamics (deflagration; detonation; deflagration-detonation transition) and on the propagation of the air overpressure wave.
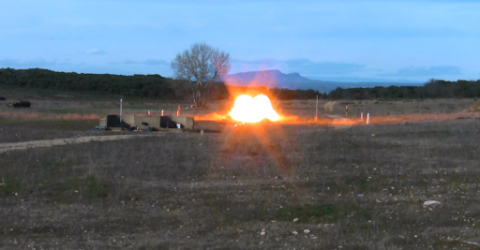
In the transport of propane, the dominant scenario leading to a BLEVE is the case of a tank caught in a fire (e.g. diesel fire). This scenario is very favourable because on the one hand the liquid propane is heated beyond its overheating limit temperature, and on the other hand because the metal wall of the tank heats up strongly and its resistance decreases. When the increase in pressure caused by the heating of the liquid exceeds the resistance of the metal, which is reduced by the heating of the walls, the tank breaks down and a BLEVE can be observed.
The tanks can be protected by a valve. This valve allows the controlling of the pressure by opening when the pressure exceeds its nominal pressure. Another effect of the valve is the cooling of the liquid. Indeed, the opening of the valve causes a drop in pressure and consequently a boiling of the liquid in order to compensate the drop in pressure. This boiling is endothermic and allows energy to be released through the valve.
Some manufacturers claim that the BLEVE can be avoided by introducing an aluminum lining into the tank. The claimed effect is that the heat from the wall is transferred to the liquid through a thermal bridge. The valve then indirectly removes the heat from the wall and keeps the temperature low enough to be safe.
The objective of this work was to test and model the influence of an aluminum lining in different thermal aggression scenarios.
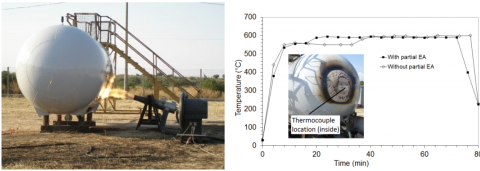
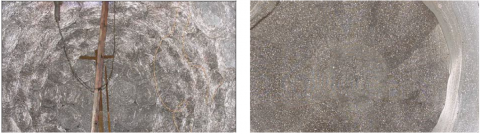
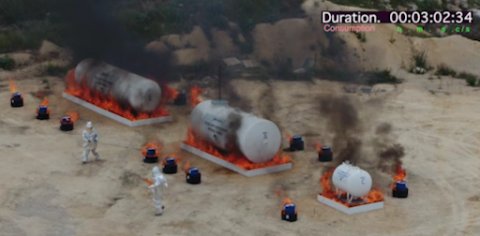
Boilover is a major industrial accident involving atmospheric storage of liquid hydrocarbons. This accidental phenomenon is described by INERIS as "...a sudden foaming phenomenon involving atmospheric tanks and resulting from the transformation into vapor of liquid water (water bottom, free water, emulsion) contained in a tank on fire". Thus, during the sudden transition from liquid water to gas, the projections of ignited fuel can generate a fireball of significant size (up to several times the diameter of the tank). The objective of this work is to study the propensity of diesel, biodiesel and HVO (Hydrotreated Vegetable Oil) feedstocks to generate a classic boilover phenomenon in the event of a tank fire by means of instrumentation allowing the precise measurement of the evolution of the temperature in the core of the hydrocarbon during its combustion.
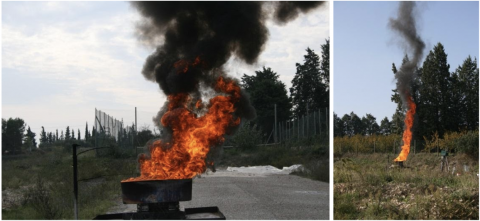
Faced with an ever-increasing demand for oil and gas, operations in the deep ocean have increased dramatically and most of the industry is looking to expand drilling into the abyssal zones. Extraction in these deepwater regions involves proven industrial risks for personnel and equipment in the event of wellhead or riser failure, which can cause loss of buoyancy of the installations due to rising gas; a polluted environment due to oil discharges; a toxic zone due to the gas cloud spreading to the ocean surface; a fire or even an explosion risk. It is therefore essential to evaluate when, how, where and how much gas rises to the surface of the ocean. This research work therefore consists of identifying physical phenomena during these accidents and modeling their physical behavior in the water column (grouping of gas bubbles or oil drops as they rise in the water column, solubilization of the products, speed of ascent to the surface, dispersion of the gas cloud in case of evaporation, etc.). The ultimate objective of this research is to develop a physical model of oil and gas leaks in the marine and atmospheric environment in order to set up scenarios according to the characteristics of the event.
